There is no doubt that South Africa is facing a water crisis, thanks to climate change, lower rainfall and a crumbling infrastructure.
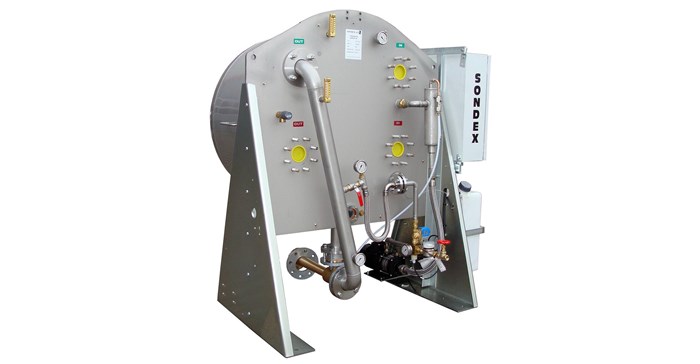
Sondex fresh-water distiller
One solution to the seriously diminishing fresh water supplies is to tap into the largest water resources available: the ocean.
Yet the reason why this seemingly obvious solution isn’t a reality is simply because desalination costs too much.
The methods of removing salt from water in order to produce process water, ultrapure or potable water are well-established, such as using membranes (reverse osmosis and nano-filtration) or thermal processes (multi-effect distillation, evaporation and crystallisation).
In thermal distillation, boiling water is turned into vapour, leaving the salt behind. The vapour is then condensed back into drinkable water when it cools down.
This process requires more energy when compared to the other common method of desalination: reverse osmosis, where seawater is forced through a semipermeable membrane that separates the salt from water.
New technology
However a Danish-based company, Sondex, has developed a process that uses heat exchangers to recycle excess or waste energy generated in an industrial process and then redirect this energy to power a separate thermal distillation plant.
“This fresh water distiller uses the waste heat from diesel engine jacket cooling water or other heat sources to produce pure drinkable water by evaporating sea water under a high vacuum, thereby enabling the feed water to evaporate at temperatures below 48°C.”
“Steam can also be used as the heat source instead of the hot jacket water. This technology eliminates the need for an additional, costly energy source,” comments Roger Rusch, CEO of IWC, an official supplier of the heat exchangers in Africa.
Two-stage design
The technology is based on a two-stage design in a vertical configuration. It is made up of two custom-designed titanium plate heat exchanger packs acting as evaporators and one titanium plate heat exchanger pack acting as a condenser. These plate packs are located in two separate chambers with different vacuums.
Stage 1
In stage one, the first evaporator plate pack, located in chamber one at 70% vacuum, turns the seawater into vapour, thereby separating the salt. This vapour is then directed through a large diameter pipe down into stage two, which is located in the second chamber working at 90% vacuum. The hot brine obtained from stage one is redirected to the second plate pack, which is also located in chamber two.
Stage 2
When the vapour reaches chamber two, it is condensed and its heat released into the second plate pack with the hot brine inside. Acting as an evaporator, the second plate pack turns the hot brine into vapour, leading to more salt separation.
The third heat exchanger pack, acting as a condenser and located in chamber two, is cooled with cold seawater and powers the custom-designed twin-ejector, which removes the non-condensable gasses and brine from the flooded evaporation process in both stages.
High-quality drinking water
The pure drinking water obtained from both stages is then directed through a flash tank, which removes any steam bubbles, and then sent to a freshwater pump, pumping the water into storage tanks.
“Each chamber is equipped with a demister that removes water drops and salt from the steam produced in stage one as well as stage two. This results in high-quality freshwater from both condensers. This system produces up to 150 tons of drinkable water per day. Typical applications are off-shore rigs, passenger ships, land-based industries located near the ocean and other places where heat is expensive to create.” adds Rusch.