
Subscribe & Follow
Advertise your job vacancies
Nordex sets sights on offering fully recyclable wind turbine blades by 2032
The Nordex Group is participating in a sustainability project, funded by the European Union, to drive the recycling of high-value rotor blade materials from wind turbine blades.

Source: Supplied
Turbine rotor blades consist of a combination of different materials such as wood, various metals, adhesives, paints, and composites. The composites are glass-fibre-reinforced plastics, as well as carbon-fibre-reinforced plastics. At the end of their life, rotor blades are challenging to recycle due to the heterogeneity of the material and the strong adhesion between the fibres and polymers. Recycling processes for these materials are not yet fully established, and reuse of recycled materials is not widespread.
“In line with our group’s Sustainability Strategy 2025, ambitious goals have been set, including offering the market a fully recyclable blade within the next decade, with the target set for 2032,” said Nordex Energy South Africa’s managing director, Compton Saunders.
EoLO-HUBS project
To reach this goal, Nordex has conducted and participated in a number of research and development projects, one of which is the European-funded ‘Wind turbine blades end of life through open HUBs for circular materials in sustainable business models’ (EoLO-HUBS).
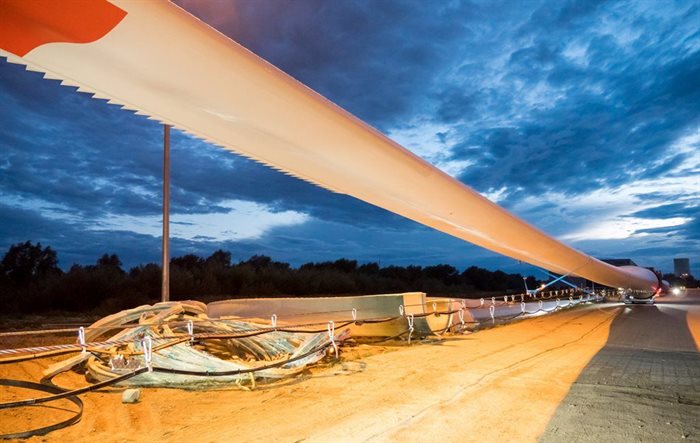
Source: Supplied
The general objective of the EoLO-HUBS project is to demonstrate and validate a set of innovative composite material recycling technologies which will provide answers to the three main areas involved in end-of-life wind farm recycling: de-comissioning and pre-treatment of wind turbine blades; sustainable fibre reclamation processes addressing two alternative routes: low carbon pyrolysis and green chemistry solvolysis; upgrading processes for the recovered fibres addressing mainly glass fibres as well as carbon fibres.
